Version 2 of CPU2 has slightly more complicated construction than it’s first incarnation. It consists of three PCBs. The base PCB holds connectors, Linux MPU module, auxiliary CPU, etc.
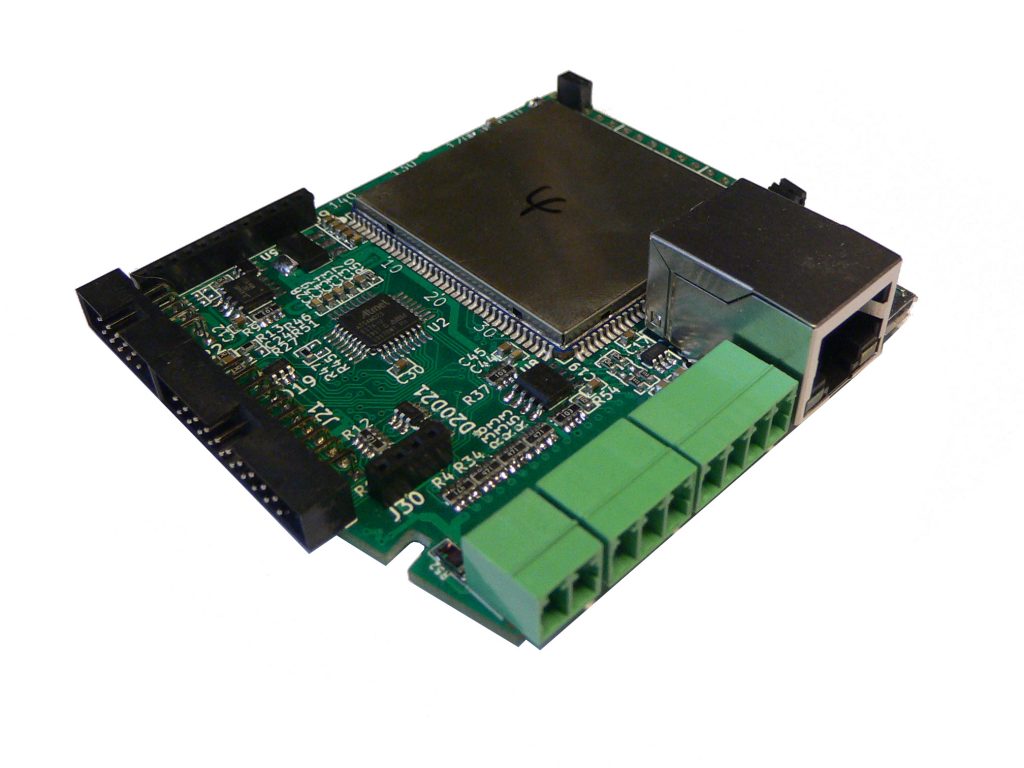
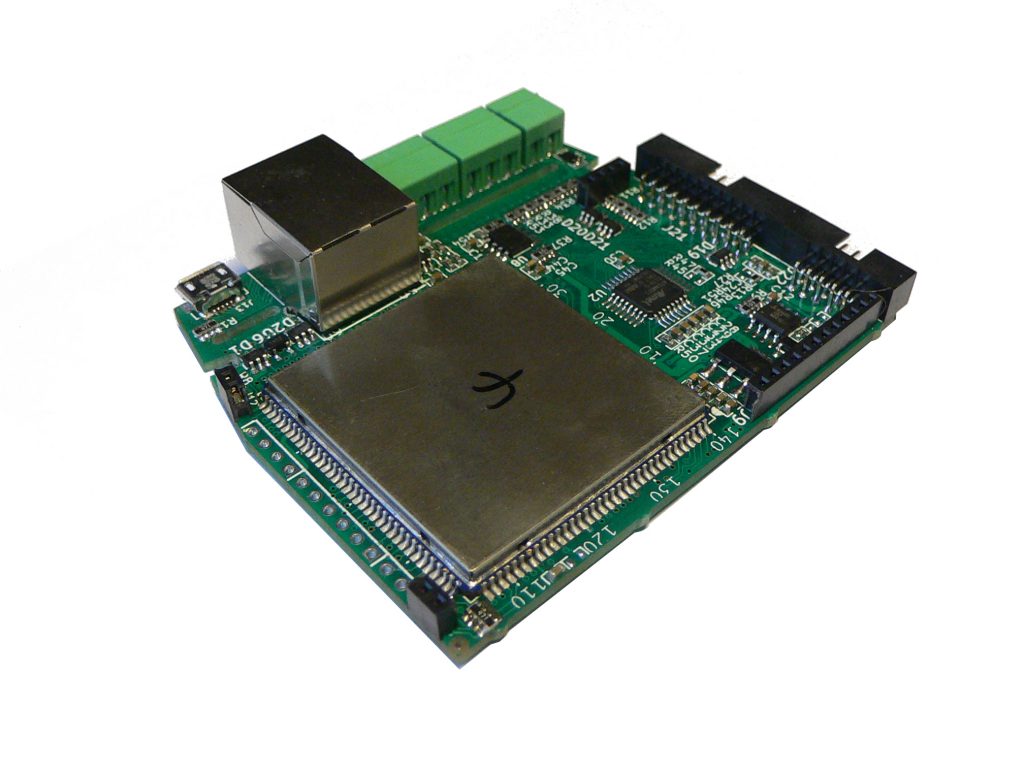
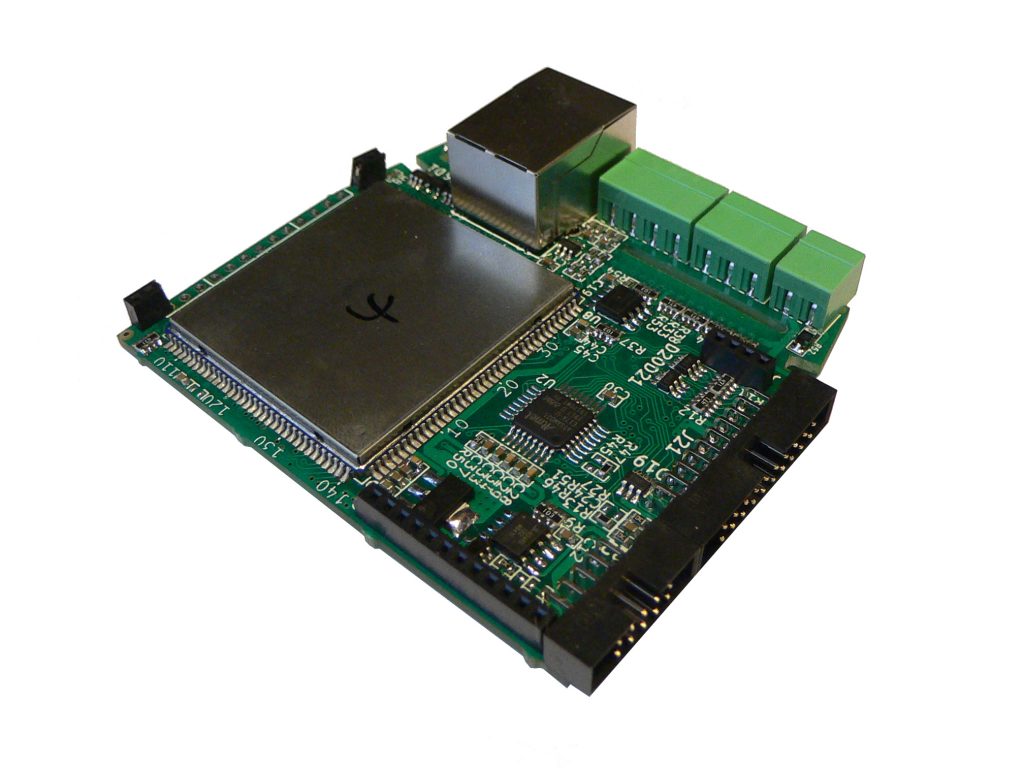
The second PCB holds LEDs, second USB and SD card slot. This slot is in a position where an inserted SD card is precisely fixed by the upper part of the enclosure (so the SD card can not jump off).
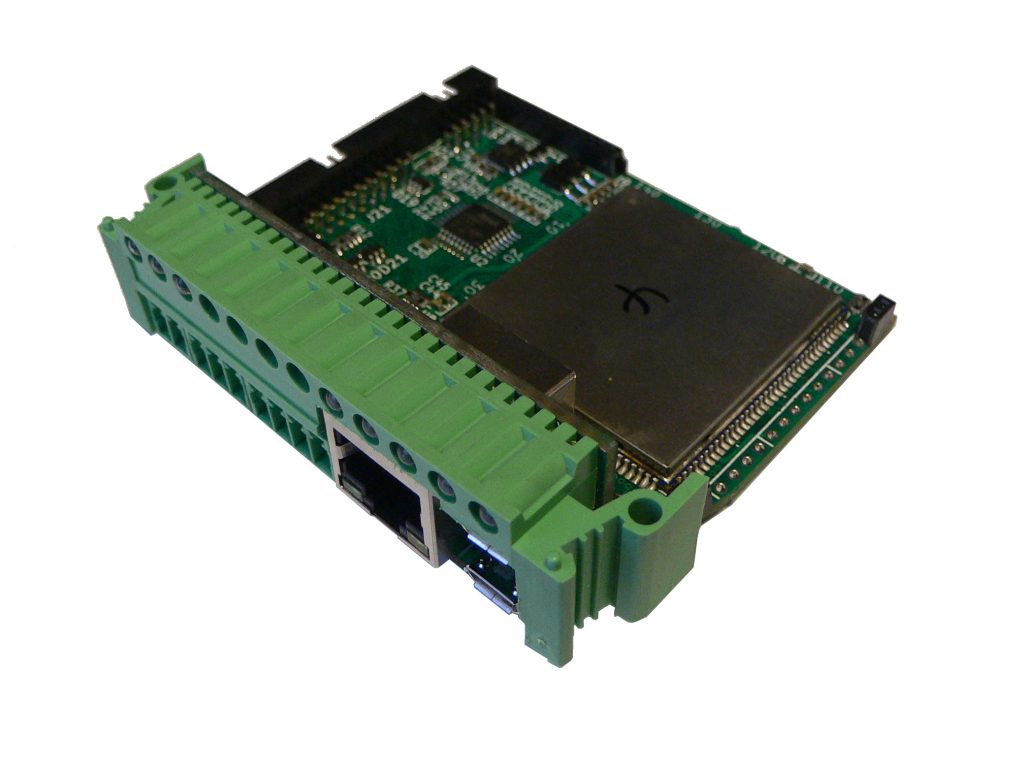

And finally there is the third PCB, which holds the power supply, backup capacitors (that allow the module to continue running for at least 10 seconds after the power disconnects), RTC with battery holder and two EEPROMs (one working and one backup).
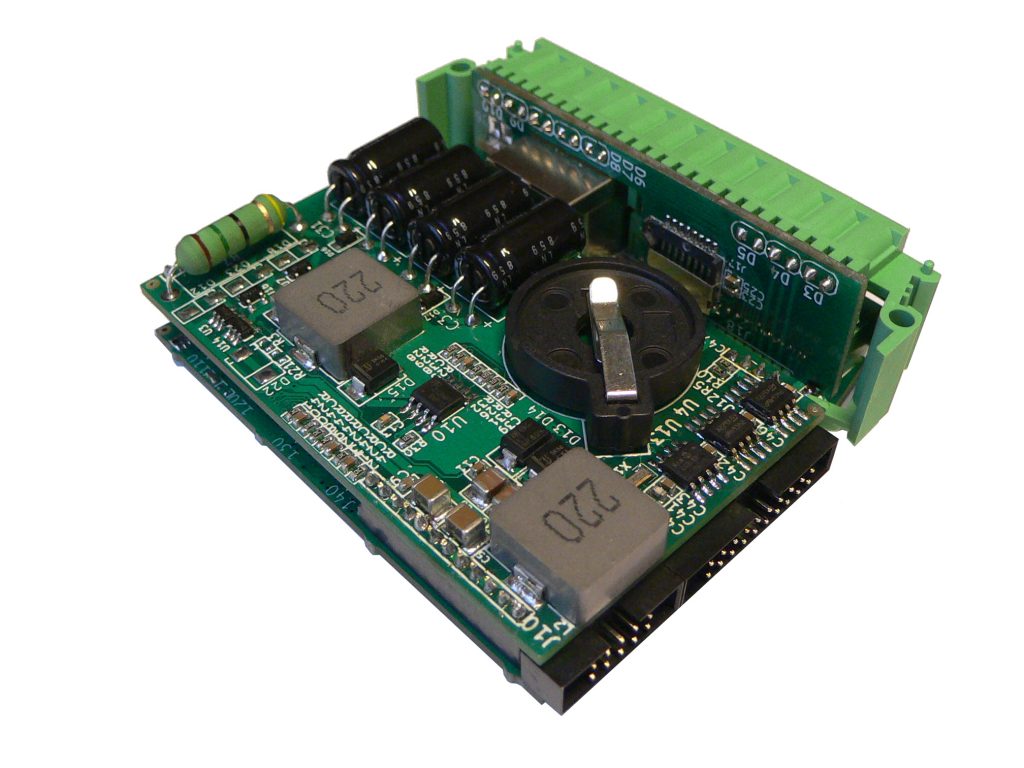
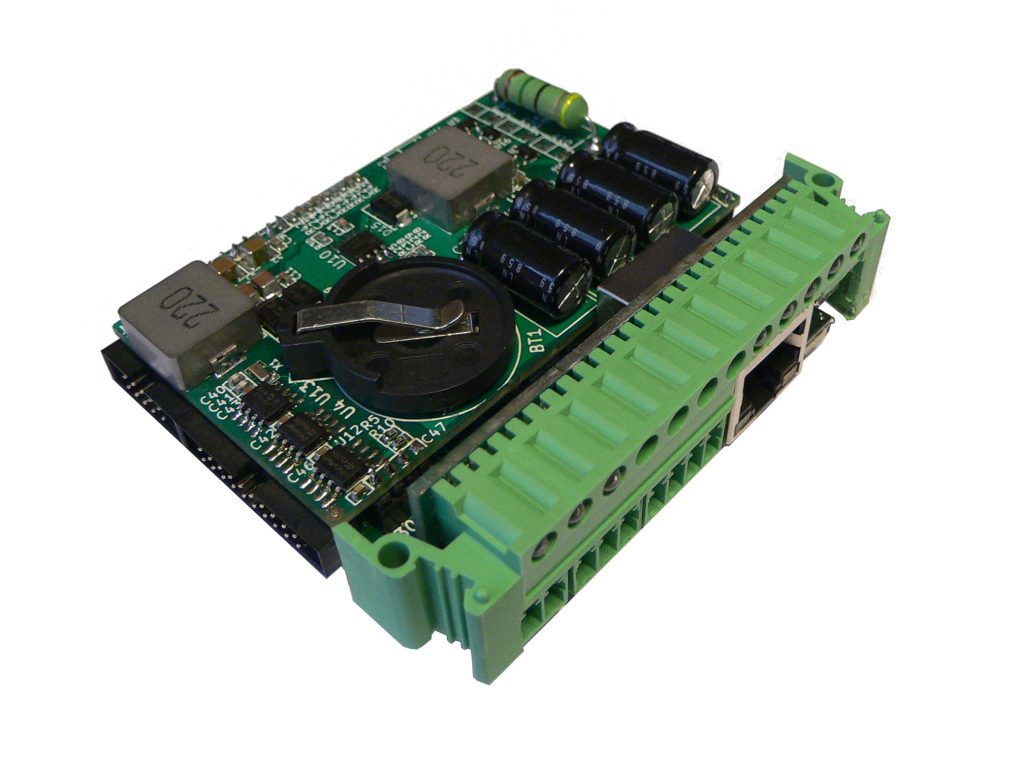
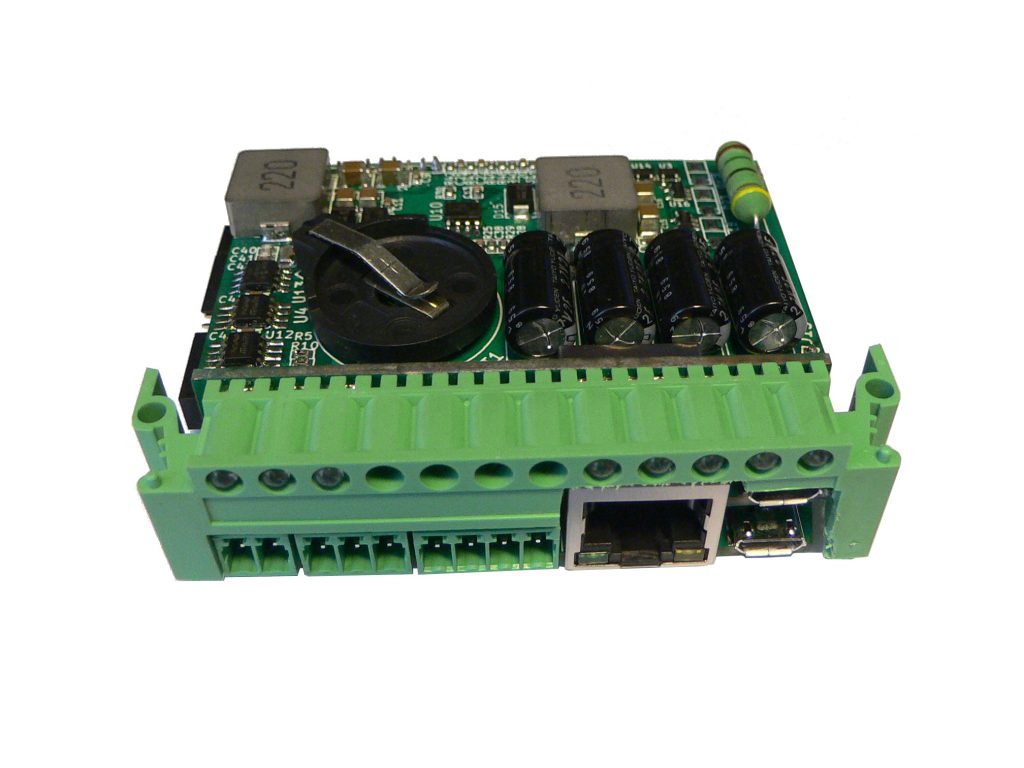
Front connectors are unchanged. From the left: power connector 24V, RS485 non-insulated, two auxiliary inputs with power output, Ethernet connector and finally two micro USBs. The first USB is directly connected to the i.MX 6 USB and can either function as a Host or as a Device. The second USB is connected to auxiliary CPU and normally is used as a UART-USB convertor for Linux system console. But with one smart option – console can be turner off, switched to read only mode (just output from Linux) or used as read/write. This USB is also used to parametrize functionality of auxiliary CPU, for reading the serial number, changing console behaviour, etc.